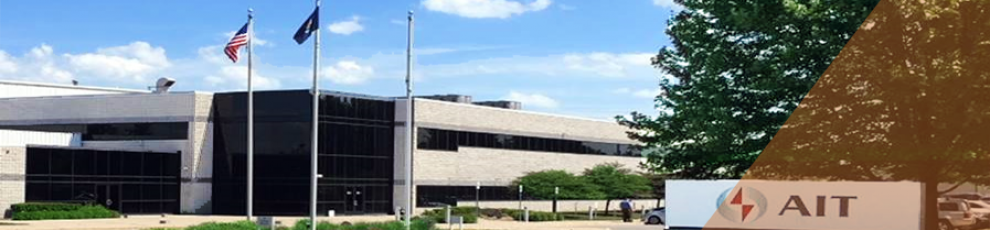
Bombardier Learjet 85 Is Coming Together In Wichita
[AIT serves as Bombardier's prime project integrator to develop the methodologies, designs and positioning systems used to join major components during final assembly of the Learjet 85 in Wichita. The inset photo shows the forward fuselage resting on one of our proprietary advanced positioning systems.]
[by Molly McMillin, The Wichita Eagle]
Bombardier Learjet 85 Is Coming Together In Wichita
The composite fuselage sections of Bombardier’s first new Learjet 85 business jet arrived in Wichita plant on a recent Saturday night.
And its arrival was met with excitement.
Alan Young, Learjet vice president of operations, came out that Saturday evening in late August to take a look.
“We all felt like handing out cigars,” Young said. “It was like the birth of a child.”
The Wichita site has been preparing to take on the project, including a major expansion, since the Learjet 85 program was announced in 2007.
Assembly, testing and customer delivery will be done in Wichita.
Sections for the second Learjet 85 fuselage — one of them 35 feet long — arrived last week.
“It’s going to have great ramp appeal,” Young said during an update on the program to local and trade journalists this week.
The two sections sent to Wichita were developed in a patented process at Bombardier’s plant in Queretaro, Mexico, then trucked north up I-35 to the plant here.
Wichita workers have completed joining the sections for the first airplane and are working on joining the fuselage for the second plane.
In another area inside the plant, mechanics are assembling the first tail section of the intercontinental eight-passenger plane.
“The fit of the parts is phenomenal,” said Ralph Acs, Bombardier vice president and general manager of the Wichita site. “The structure is coming together nicely.”
Structural testing will be done by Wichita State University’s National Institute for Aviation Research.
The company is working closely with suppliers.
Once something is sent and installed, “I don’t want to take it off again,” Acs said was his message to suppliers.
They’re using a system integration rig to work with suppliers to refine and mature the Learjet 85’s software and systems with systems integration testing.
The local Learjet site is in the midst of its largest expansion to date.
It expanded the factory to make room for the airplane and completed construction of new parking.
Work on a production flight test building is under way.
It also will add a new paint facility and delivery center.
“It’s a big expansion,” Acs said.
The Wichita site employs about 3,000.
The company is pleased with the quality of work coming from its Queretaro plant, Acs said.
“The quality that comes out of there is equivalent of the quality you will get from any of our sites,” he said.
The 185,000-square-foot Learjet 85 component manufacturing facility was completed in July 2010 to build the plane’s major structures.
One of the reasons the site was chosen is because Queretaro is one of the safest locations in Mexico, Acs said of the centrally located city.
The Learjet 85 is just one example of the company’s investment in new product development.
Officials this summer said that they will replace the Learjet 40 and Learjet 45 with the Learjet 70 and 75.
But there remains a hold in the product line-up between the Learjet 75 and the Learjet 85, Acs said.
“I think there’s an opportunity between the 75 and the 85,” Acs said.
He alluded to a Learjet 85 derivative.
The notion in designing the all-new platform is to be able to “spin that into other things,” he said.
“So a Learjet 80?” one journalist at the briefing asked.
“It could be an 81,” Acs said, jokingly. “It could be a 90.”